Contact us
Come and visit our showrooms to see the full range.
SQUARE METRE FLOORING SHOWROOMS
Fulham Showroom:
Address: 875 Fulham Road, SW6 5HP
Email: sales@sqmflooring.co.uk
Phone: 02077368789
Opening times: Monday - Friday (9AM - 5:30PM), Saturday (10AM - 5PM), Sunday (Closed)
Belsize Park Showroom:
Address: 77 Haverstock Hill, NW3 4SL
Email: belsizepark@sqmflooring.co.uk
Phone: 02073621349
Opening times: Monday - Friday (10AM - 6PM), Saturday (10AM - 5PM), Sunday (Closed)
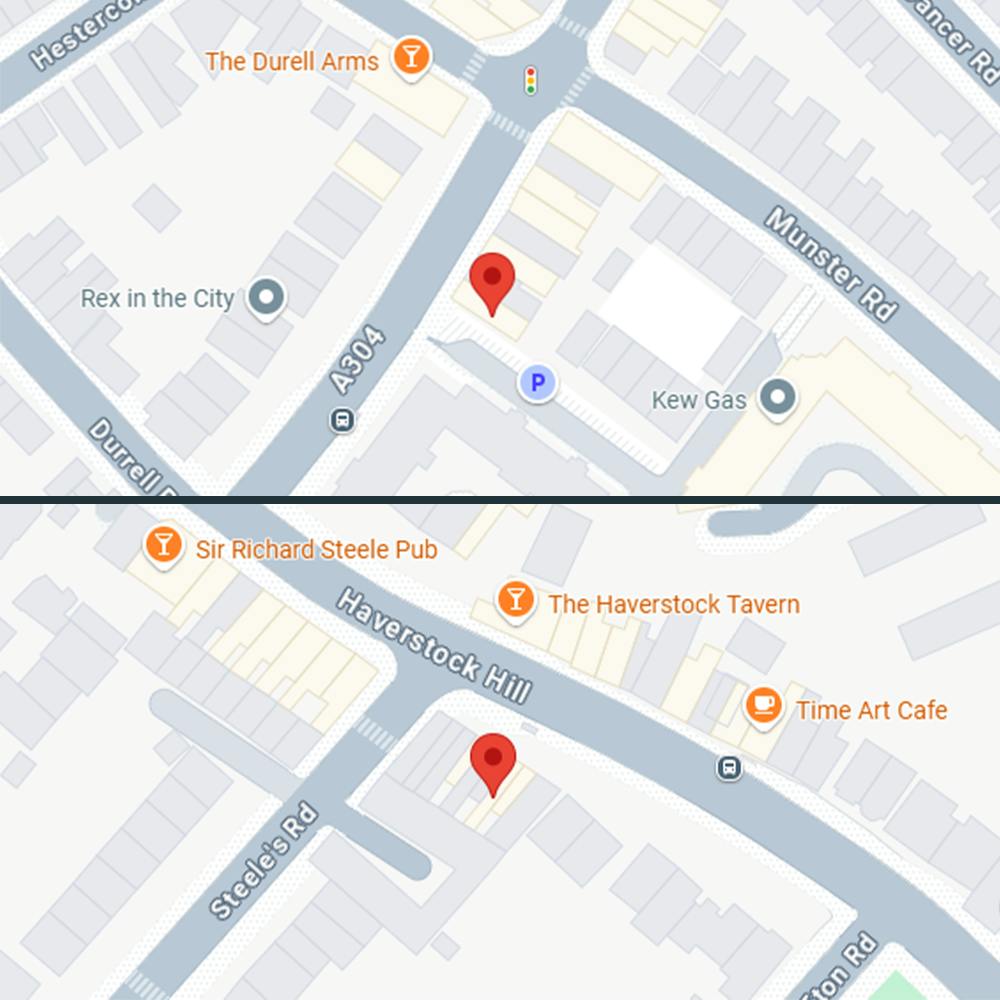
Help & Support
At Square Metre Flooring, we want our customers journey to be as seamless as possible.
We understand that a renovation journey can be as exciting as it stressful. As a result, our team has been trained to be as helpful, informative, compassionate as possible.
We offer a huge amount flexibility to ensure we can accommodate the specific nature of every project. We understand that no two projects are the same and we endeavour to be there for you on this journey.
See below help links for any queries you might have. If you still require any further assistance or would prefer to talk to a member of our team, kindly contact us using the details above.
FAQs
At Square Metre Flooring, we want our customers journey to be as seamless as possible. We understand that a renovation journey can be as exciting as it stressful. As a result, our team has been trained to be as helpful, informative, compassionate as possible.
- We offer a huge amount flexibility to ensure we can accommodate the specific nature of every project.
- We understand that no two projects are the same and we endeavour to be there for you on this journey.
See below help links for any queries you might have. If you still require any further assistance or would prefer to talk to a member of our team, kindly contact us using the below:
01 What is the different Grade of Flooring?
AB Select/Nature grade flooring is handpicked to contain small knots giving a cleaner look. Variation in colour, grain and sapwood around the edge of the board is still apparent adding to the natural effect.
Rustic/Classic grade flooring allows for a wide variance in colour, tone, grain and knot content. You will see Sap Wood, Heart Wood and natural shakes. Being a natural product, you will also get splits and dead knots within the timber which are normal and filled with either a black or brown resin. We strongly recommend you look at our room set photos and featured installations to really appreciate the rustic character in all its beauty.
ABC Mixed grade is popular in species such as walnut. This grade displays more variation in grain and colour with larger knots and more sapwood well distributed. Small filled cracks and dark streaks are also apparent.
Extra Rustic Grade. Very little is graded out of this category. Large knots, cracks and splits will be visible. There is any amount of sapwood that makes this a fun choice and mean that your floor will be more distinctive and characterful.
02 What are the different surface finishes available?
Brushed: A steel brush removes the soft grain from the surface layer creating a textured surface which enhances the beauty of the natural grain. Brushing is often used with stained products.
Distressed: To create this effect various methods are used to give the wood an aged, well used appearance also that of a board milled using rudimentary rustic tools. The skill is in making the distressing look natural.
Stained: Stain is applied by rollers and buffed in to penetrate the top surface of the board and then sealed with either oil or lacquer creating some stand out floors.
Smoked: Timber is stored in drying rooms filled with ammonia vapor or “smoke” for up to 3 days until the wood colour darkens. This means that the floor keeps its rich colour even after refinishing.
Cross Sawn: Random saw marks are made across the grain to add an extra texture to the surface.
Unfinished: Could anything feel more natural and authentic? An unfinished floor also gives you the chance to create a bespoke finish by painting, oiling or varnishing exactly how you wish. Unfinished boards are supplied with the knots pre-filled, and are pre-sanded for your convenience.
Hand-scraped: This finish sees each plank painstakingly scraped by hand, bringing a whole new dimension to your natural floor. The irregular ridges and grooves that result add depth and definition to the wood’s surface, creating an aged look that’s distinctive by eye yet smooth to the touch.
Bevelled Edge: A bevelled edge on the boards creates a defined pattern across your floor when it’s fitted. The finish gives a traditional and ordered feel to a space and the depth of the slight groove between planks will depend on the type and grade of wood you choose.
Planed: Planed boards are finely sanded using up to six careful processes in order to create a delightfully smooth finish across the boards. Small and subtle ribbing marks are still visible from the planer for an authentic yet contemporary look.
Square Edge: Fitting seamlessly together, square edged planks result in smooth, clean overall finish to your floor, and can help a room to feel bigger than it is. This finish suits modern décor very well, while the wood’s clean finish takes you away to a relaxing natural setting.
03 What do I need to do before floor installation?
Before Delivery
The conditions must be ideal before any flooring is laid. Wet trades like concreting, plastering and decorating need to be complete and the building must be thoroughly dried out. Windows and doors should be fitted and watertight.
A rule of thumb for the drying time of a sand and cement-based screed is one day per millimetre for the first 50mm, and 2.5 days for each millimetre thereafter. So, a 50mm screed should take about two months to dry out, and a 100mm screed will take six months. Plaster takes up to six weeks to dry completely.
Preparing the Subfloor
The surface immediately beneath a natural wood floor must be in good structural condition, free from damp rot, fungal or insect infestation, and contaminating residues. It must be flat with bumps and dips not exceeding 3mm over a 2m area. Naturally, the surface should be vacuumed and totally free of debris before fitting begins. Hot pipes should be well insulated to prevent localised hotspots, which can cause wood flooring to warp or shrink.
N.B - The subfloor should be prepared for installation in accordance with the industry standards outlined in BS-8201-2011.
Heating and Air Conditioning
The room temperature and humidity levels need to be stable before Woodpecker flooring is delivered to site. Heating and/or air conditioning systems should be on and working for at least two weeks before the floor is laid. If underfloor heating is present, multi-layered planks such as Engineered board, Bamboo or vinyl should be chosen over Solid Wood as these provide better stability. Install solid wood flooring over an underfloor heating system at your own risk!
Atmospheric Conditions
The room temperature shouldn’t be lower than 18°C (64°F), with a floor temperature higher than 15°C (59°F). The Atmospheric Relative Humidity should be between 40 and 60%. Note that wood floors are not suitable for wet rooms, or in areas where there is a regular flow of water.
Acclimatisation
Nature is in no hurry when it produces trees, and likewise, an impressive wood floor installation is never rushed. The sealed, unopened boxes should be laid flat, in the centre of the room for a period of time beforehand. Vinyl will acclimatise over 24 hours, Engineered and Bamboo flooring takes three or four days, and solid wood requires five to seven days. DO NOT store the flooring outdoors, in an outbuilding, or anywhere with damp or condensation problems. The conditions where the flooring is acclimatised should be as close as possible to the typical living conditions.
Inspection
At Square Metre Flooring, the highest quality control procedures are in place, however our products are made from natural materials so it’s essential that every plank is carefully checked before installation. If there are any problems, get in touch with us so that we can rectify them. We can’t consider any defects after the floor has been installed.
Laying the Floor
The natural texture of wood flooring will really come to the fore if the planks are laid in the same direction as the light entering the room. However, if the flooring is being laid over existing parquet, it should be positioned at right angles to the previous flooring planks.
Disclaimer: Installation guidance is advisory and is based on established good practice and the BS-8201-2011 standard. It is the fitter’s responsibility to follow these procedures before, during and after installation. Square Metre Flooring cannot accept responsibility for any issues relating to installation.
Moisture Testing
Moisture is the enemy of natural wood, and can damage your beautiful flooring. Even when your subfloor looks dry, it may contain excess moisture in the substrate. Using a professional moisture meter such as the Protimeter MMS will tell you whether or not it’s safe to go ahead with installation. Readings shouldn’t exceed:
- 70% Relative Humidity (RH) for cement-based concrete
- 11% Wood Moisture Equivalent (WME) for wooden subfloors or joists.
04 What is the checklist for using adhesive?
Is everything dry? The plaster in the room and cement subfloor should be completely dry before the wood floor is fitted. The drying time for a cement-based screed is one day per millimetre for the first 50mm and 2.5 days per millimetre thereafter.
Is the subfloor level? If the subfloor needs to be levelled, apply our Level-X™ Primer followed by Level-X ™ Self-Levelling Compound, which is fibre reinforced. Never use latex self-levelling compounds. They lack the tensile strength to resist the movement of the timber.
Is the subfloor within moisture tolerance? A cement-based screed must have a Relative Humidity (RH) reading of 70% or less. If not, always use Woodpecker WP60 Liquid Damp Proof Membrane which seals the moisture below the surface preventing the wood from absorbing it and expanding or distorting. Make sure the floor is completely free of dust and contaminants before applying the damp proof. Wooden subfloor readings need to be between 7 and 11% Wood Moisture Equivalent (WME).
Has the wood acclimatised? Wood flooring must be left to acclimatise before fitting. To do this, place the packs in the centre of the room where the flooring will be laid. Test its wood moisture level and make sure it is similar to that of the wooden subfloor before fitting to prevent undue expansion or contraction. If the moisture readings aren’t close, use a different method to fit the flooring.
What is the Atmospheric Humidity in the room? It should be between 40 and 60%.
Is there underfloor heating? If so, it must be thoroughly tested, and turned off 48 hours before fitting.
05 What do I need for a floating installation?
Is everything dry? The plaster in the room and cement subfloor should be completely dry before fitting the flooring. The drying time for a cement-based screed is one day per millimetre for the first 50mm and 2.5 days per millimetre thereafter.
Is the subfloor level? If the subfloor needs to be levelled, apply our Level-X™ Primer followed by Level-X ™ Self-Levelling Compound, which is fibre reinforced. Never use latex self-levelling compounds. They lack the tensile strength to resist the movement of the timber. Minor undulations can be disguised using the XL Underlay.
Is the subfloor within moisture tolerance? A cement-based screed must have a Relative Humidity (RH) reading of 70% or less. Wooden subfloor readings need to be between 7 and 11% Wood Moisture Equivalent (WME). If there’s any doubt about moisture levels in the subfloor, use an underlay with an integral damp proof membrane and lay this with the barrier side down to form a protective layer.
Has the wood acclimatised? Never unload the flooring and start fitting. It should acclimatise in the centre of the room where it’s going to be laid. Vinyl floors will acclimatise over 24 hours, Engineered and Bamboo flooring takes three or four days, and Solid Wood requires five to seven days.
What is the Atmospheric Humidity in the room? It should be between 40 and 60%.
Is there underfloor heating? If so, it must be thoroughly tested, and turned off 48 hours before fitting.
06 How do I choose a floor that works with Underfloor Heating?
Choosing a floor
Just like a natural wooden floor, underfloor heating helps make a room feel comfortable and cosy. However, if you have underfloor heating, it’s important you choose the right wooden floor to go with it. We always recommend an Engineered board rather than Solid Wood. It will give you increased stability and strength to withstand changes in temperature thanks to its multi-layered construction.
Not all timbers react well to underfloor heating, but the good news is that each type of flooring in this catalogue carries a recommendation with it so you’ll easily be able to tell which ones are suitable, and which aren’t.
Checking the Subfloor
Never install underfloor heating over a concrete subfloor that has a moisture content over 75% Relative Humidity (RH). Ideally it should be below 70% RH to give a margin of error.
If there is a timber subfloor, make sure the moisture content is below 11% Wood Moisture Equivalent (WME). These readings must be checked before fitting. If the moisture levels in the subfloor are too high, install a Woodpecker damp proof preparation product before the underfloor heating is fitted.
Choosing a System
If you are installing an underfloor heating system before fitting a natural wood floor, there are two types available – water heated, and electrically heated.
In general, water heated systems are used in new builds and in renovation projects, while electrically heated systems are used when installation needs to be relatively quick and easy.
Whichever system you choose, the maximum temperature of the water or the electrical element must never rise above 50°C, and the temperature to the underside of the wood floor must never reach more than 27°C.
Testing the Heating
Once the underfloor heating is in place it should be switched on and thoroughly tested before the wood floor is fitted. A water-heated system needs to be pressurised, checked for leaks, and left to run for two weeks. It will dry out much of the moisture in the screed or timber subfloor.
Plastering and any other wet trade in the room must also be dried out and the Atmospheric Humidity in the room should be between 40 and 60%.
Fitting the Floor
Turn off the underfloor heating for at least 48 hours prior to fitting the floor – the regular central heating or electrical heating can be left on during installation.
If a screed or wood-based subfloor has been laid above the underfloor heating system, you can glue an engineered tongue and groove floor to it. Make sure the boards are fully adhered to the subfloor using Woodpecker MS Parquet Adhesive.
An Engineered floor with glue-less locking joints can be floated over underfloor heating in most cases, but be certain to use an underlay that’s suitable for an underfloor heating system.
If only part of the subfloor has underfloor heating, you will need to separate the wood flooring above the heated and unheated areas using a dilation joint. Flooring above the underfloor heating will expand and contract more than the flooring that isn’t, but the joint will accommodate that.
Aftercare
Once fitted, the floor should be left to acclimatise for two to three days before the underfloor heating is turned on. This will allow it to settle and any adhesives used can dry out. When the heating is switched on it should be set at 1°C above the ambient temperature and then raised by a further 1°C per day until the desired temperature is reached. Do not turn it on full straight away. Raising and lowering the temperature too quickly can cause the wood to shrink, expand or even crack.
This method of gradually changing room temperatures should be continued, with the underfloor heating left running from the thermostat at all times and only raised or lowered by 1°C per day to accommodate the changing seasons.
These guidelines are here to help make sure you protect your natural wood floor but they don’t replace the recommended fitting procedures for your underfloor heating system, which vary by manufacturer.
07 What Daily care can I carry out to maintain my floor?
Once your floor has been installed, you’ll be able to feel its delightful texture underfoot and enjoy the warm sense of nature a wood finish brings to your home. However, like all natural substances, wood is susceptible to wear and tear. To ensure it always looks its best and lasts longer, here are some steps you can take to protect it…
Floor mats
The natural place to start is at the door, and a good quality floor mat will catch dirt and grit, preventing damage further into to your home. Grit underfoot is like sandpaper, scratching the floor’s finish, so consider fitting Woodpecker Coir Matting which provides a barrier to wet and dirty feet.
Rugs or carpet runners
We know that the last thing you want to do is cover up the beautiful texture of your natural wood floor, but sometimes prevention is better than the cure. Consider rugs or carpet runners for high footfall areas such as doorways, halls and stairs.
Be careful with furniture
Never drag furniture or other objects across your wood floor – it can easily result in unsightly dents or scratches. Woodpecker offers a variety of felt protectors and castor cups that enable you to move furniture easily without markingyour floor.
Shoe rules
Avoid wearing heavy shoes or work boots when stepping onto your natural wood floor. High heels, and stilettoes in particular, should be avoided. They exert a huge amount of pressure that easily dents or marks even the toughest of wood floors.
Clean up spills
Liquid is the enemy, so mop up any spilled drinks and never allow water or other liquids to sit for any length of time. The odd drop may not hurt, but excessive amounts of water will cause lasting damage.
Pet patrol
Nothing’s more natural than a dog or cat curled up by the fire, asleep on your wood floor. But remember to keep your pet’s claws trimmed to prevent scratches and, as with point five, if there are any ‘accidents’ make sure they’re cleaned up fast.
Sunshine
It’s thrilling to see the sun illuminating a wood floor, filling the room with natural light and warmth. Sunlight will naturally help the wood’s colour to mellow, so be aware of this and move rugs, mats and furniture regularly to ensure an even maturing of colour. Dark woods like Walnut are more susceptible to fading, which is worth considering when you choose your flooring.
Light cleaning
Regular sweeping with a soft bristled broom will get rid of dust and rogue bits of grit on the floor. You can also vacuum a natural wood floor – ideally with a soft brush attachment to minimise scratching.
Mopping
As per point five, wetness can damage a hardwood floor so always use a well-wrung mop when cleaning and remove excess liquid immediately. Woodpecker supplies specially formulated cleaning kits that include an antistatic mop, cleaning fluid and trigger head spray bottle for easy application. They are available for both lacquered and oiled finishes, with refills available as necessary.
08 What Long term care is available?
Long Term Care
Even though the most advanced wood treatments and finishes are used to create our nature inspired flooring, your hardwood floor will need to be looked after to stay in tip-top condition. This involves cleaning and sometimes re-finishing your flooring at suitable intervals to ensure it continues to delight throughout its lifetime.
Cleaning Oiled Floors
To protect the beautiful look and feel of your oiled floor, we recommend removing grit and dust regularly with a brush or vacuum cleaner. You can also use the Woodpecker Cleaning Kit for Oiled Floors or a well wrung dampcloth mop.
For a deeper clean now and again, use Woodpecker One Coat Soap. This clever product will clean your floor and form a protective film, helping to build its surface resistance over time and making your floor even easier to maintain.
Cleaning Lacquered Floors
Ensure your lacquered floor stays clean and keeps its stunning shine by using the Woodpecker Cleaning Kit for Lacquered, Laminate & Vinyl Floors or a well wrung damp mop.
Restoration Treatments for Wood Flooring
How often you recoat or repair your floor will depend on several factors including the type of floor it is, its finish and the wear its experienced. However, as a basic preventative, you might consider recoating your floor every two or three years. Don’t wait until your floor looks worn. If you allow the protective coat to wear away, it becomes susceptible to dirt and water penetration and harder to clean and repair.
A Quick Test
A good way to check whether your floor needs treatment is to pour a few drops of water onto its surface. If the finish is in good order, the water will bead on the floor and can easily be wiped way. No maintenance is needed. If the water slowly soaks into the timber, leaving behind a light saturation mark, the finish is starting to wear thin. A new coat of lacquer or oil should be applied. However, if the water is immediately absorbed and leaves a dark stain, the finish has been completely worn away and the floor may need sanding and recoating.
NB: Before any treatment is carried out, we recommend testing in an inconspicuous area of the floor to check compatibility.
Brecon/Vinly Floor Repairs
The best way to conceal small scratches and marks on our Brecon range is with Scratch fix – a quick and easy method to restore scratches on resilient floors.
Re-lacquering and Repairs
If your lacquered floor gets any isolated scratches or dents, these can be sealed using Woodpecker Touch-Up Lacquer or any of our other flooring repair products. First, make sure the area is clean and dry then lightly sand the surface with a fine grit sanding paper. Using the brush supplied in the lid, paint the lacquer onto the affected area and leave it to cure.
Deeper scratches or gouges might call for professional wood filler. These are available in a variety of colours from most hardware and flooring retailers. They come as a paste, which is applied to the damaged area, left to cure, then sanded. Afterwards, apply some Woodpecker Touch-Up Lacquer to give the repair a protective finish.
Extra care is needed when sanding stained floors to ensure that the process doesn’t break through the complete layer of stain. In this instance, the floor would require a patch-repair before the lacquer is applied.
If the floor is badly worn in some places, it may be necessary to sand the flooring back to its unfinished surface before recoating all over. Unlike oil, lacquer doesn’t penetrate the wood’s surface, instead it sticks to it. Therefore, the entire floor must be covered to prevent the formation of ridges and overlap marks. For best results, use a roller. A single coat of lacquer will be enough to protect against moisture, though several coats should be applied if the floor faces lots of foot traffic.
If you are lacquering unfinished timber, you will need to cover it with three coats. Between each coat, the floor must be sanded, vacuumed and wiped thoroughly with a damp cloth. Lacquer takes one to two hours to dry between applications. After the final coat, leave the floor for 24 hours before stepping onto it. Curing will continue for a week, after which rugs can be placed onthe floor.
Re-oiling and Repairs
Unlike lacquered floors, isolated areas of an oiled floor can be treated without having to re-oil the entire floor. Yet, oiled surfaces aren’t as tough as lacquered surfaces and need to be maintained more often.
Before re-oiling your floor, it’s essential that you clean up any dust or dirt that’s accumulated. Contamination will hinder adhesion and could affect how the floor looks. Apply a small amount of One Coat Cleaner to a dry cloth and wipe the affected area thoroughly. Dust will be collected electro-statically. It takes 15 minutes to an hour to dry depending on the saturation. If the floor remains soiled, consider sanding the surface and clean again with One Coat Cleaner.
Make sure the floor is completely dry before applying Woodpecker One Coat Oil. This should be applied sparely and evenly, along the wood’s grain, using a cotton cloth, brush or squeegee. The oil will react with the floor within a minute and any excess should be wiped away within 15 or 20 minutes making sure the surface is nearly dry. It’s a good idea to treat relatively small areas each time because the oil reacts quickly. Oil doesn’t leave tide or overlap marks and should be left for 24 to 36 hours before you can stand on the floor again or it’s cleaned.
09 Should I fit my floor before the kitchen?
We always recommend that the floor installation is the last part of your building or renovation project. Whilst it may be simpler to install fitted furniture like a kitchen on top of a floor it is not a good idea. A wood floor will expand and contract with variations in climate which is why an expansion gap is created around the perimeter of an installed floor. For this reason, we advise against pinning the floor down with heavy kitchen fittings and work tops. If a floor is pinned down then it can cause uneven expansion which in turn can cause the floor to exceed perimeter gaps in certain areas. Ideally the kitchen should be installed and the floor should be fitted up to the cabinets using the kick boards and undercutting of end panels or pillars to cover the expansion gap.
Privacy Policy
OpenClose
Our Privacy Policy outlines the policies of Square Metre Flooring, 875 Fulham Road, London, SW6 5HP, United Kingston of Great Britain and Northern Ireland, email: sales@sqmflooring.co.uk, phone 02077368789, on the acquisition, utilisation and impartation of your information that we gather when you utilise our website (https://sqmflooring.co.uk). By using this website, you are agreeing to the gathering, utilisation and impartation of your information in alignment with this Privacy Policy. If you do not agree with these policies, please do not use this website/service.
This Privacy Policy may be altered at any point by us without providing notice to you and we will display the new Privacy Policy on our website. The new policy will be in use 180 days from when it is posted on the website and any further use of the website on your part after these changes will establish your acceptance of the new Privacy Policy. Therefore, it is advised that this page is reviewed regularly.
Information we collect about You:
The obtaining and utilisation of Personal Information means any information that may be used as a means of identification, such as your name, home address, email address, phone number or title. For the most part, you can search through our website without disclosing any personal information. A few products are utilised to investigate website influx so that we can constantly improve our website for you and gauge with your needs. Nevertheless, there are other actions on our website that will need you to register with us. Such as: making an online purchase, signing up to our newsletter and having samples ordered to your home. The registration process is one of the ways in which we collect information. That information is used for a few reasons: to reaffirm that our records are correct and to keep our customers happy, to keep people up-to-date with the latest design styles if you’ve asked to be informed and to contact you in case we need to give or attain any more information.
If you use our website, we may obtain the following personal information from you:
- Name
- Mobile and/or Home Number
- Email Address
- Home Address
- Company Information
- Payment Information
How We Gather Information:
We obtain information about you as follows:
- Mailing List Sign-Up
- Checkout Process
- Registration Forms
- From Public Sources
- Interactions With the Website
- Any Time a User Submits Information
How We Work with Your Information:
We will use your information for:
- Creating a User Account
- Customer Feedback
- Targeted Advertising
- Support
- Processing payment(s)
- Testimonials
- Marketing/Promotions
On the rare occasion that your information may be used to any other effect, we will ask for your approval. We will use your information only after receiving your approval, and then, only for the purpose(s) for which you granted approval unless we are required to do otherwise by law.
How We Impart Your Information:
Your personal information will not be shared with any third party without us asking for your permission, except in special circumstances which you can see below:
- Data Gathering and Processing (through the website visitor disclosing information and Cookies – find more information listed below)
- Analytics (through Cookies – find more information below)
- Promotion/Advertising Services (through Cookies – find more information below)
Third parties will utilise the personal information that we share with them solely for the objective for which it was originally shared. They shall not hold this information for longer than is needed to accomplish such objectives.
Your personal information may also be transferred for these reasons:
- To adhere to relevant, appropriate law, court order, regulation and other legal actions.
- To administer your agreements with us (including this Privacy Policy).
- Lastly, to reply to declarations that your utilisation of the website breaches any third-party rights.
Should our company or the website be joined with another company, your information will be one of the resources that is given to the new owner.
Cookies and Third-Party Policy:
Cookies are minute files consisting of information that a website passes to your computer’s hard disk for its own records and allows us to evaluate our site transit tendencies. Cookies can’t give us admittance to information other than what you provide us with; they also cannot give us access to your computer. A lot of web browsers accordingly accept cookies without you having to do anything; check your online help or browser’s manual if you want information on changing how the browser deals with cookies. If cookies are disabled, one can still see the information on our website which is available to the public. Moreover, if you are sharing a computer and you have cookies switched on, make sure to log off when you are done.
Google Analytics:
If you choose to visit our website, we used a third-party service (Google Analytics) to amass data and information about of visitor behavioural tendencies. This is done to discover things such as the number of visitors to various parts of the website. Such information is only used in a that nobody is identified.
Mailing Lists:
We obtain personal information for our newsletter. This information is used for various reasons: to contact you if we need to gather more information, to check that our data is correct, to check periodically that you are content with our services and to inform you about matters you have asked about. Lending or trading our email lists with other companies does not take place. A third-party provider is used by us to publish our newsletter. Statistics on clicks and email opening are stored using certain technologies in order to enable us to oversee, check and reform our newsletter. If you wish to unsubscribe from our mailings at any time, please email us at: sales@sqmflooring.co.uk.
Advertising:
A Google Ads Tracking Code and Facebook Pixel are used on our website (UK and US sites) to transfer helpful information back to Google and Facebook about how our website visitors are using the websites. That information may then be utilised to show more appropriate content by way of paid advertising to visitors/users who have interfaced with our website in the past, or to those who may be comparable viewers. We do not vend or give this information to any other companies and personal data is not stored or compiled in the tracking code or Pixel. This data and information are only used to provide a more valuable, idoneous and smooth-running experience for you.
Rights and Opt-Out:
The right to alter, amend and/or delete, look at any of your personal information that we keep on file is obviously reserved by you. Please email sales@sqmflooring.co.uk if you have any requests.
Opting out of any of the profiling we carry out for commerce purposes or direct commerce communications is also an option for you. Please email sales@sqmflooring.co.uk for this matter.
Please acknowledge that if you do opt out to us processing/gathering the necessary personal information, you might not be able to have means of entry to or you may not be able to use the services for which your information was potentially needed.
The Storing of Your Information:
Your information will be held by us for 90 days to 2 years after users close their accounts or for as long as is required for us to meet the objectives for which it was gathered as written in this Privacy Policy. Some information may have to be held by us for longer amounts of time for purposes such as keeping records/reporting in compliance with appropriate law or for other valid reasons such as law carrying-out of legal rights, preventing fraud etc. Anonymous information which does not identify you, may be kept indefinitely.
Data Protection/Queries:
Should you have any worries or questions about the treatment of your data, you may email us at sales@sqmflooring.co.uk. We shall undertake your worries in compliance with appropriate law.
Delivery, Exchange & Refund Policy
OpenClose
DELIVERY
When will I receive my floor?
All deliveries are on a 2-3 working day timescale from the date that an order is placed, subject to stock levels. While every effort is made to ensure that all items shown on the website are in stock, we offer no guarantee of availability and this electronic publication does not constitute an offer for sale. A member of our team will be in touch on receipt on your order to confirm stock levels and delivery availability.
The above 2-3 working days standard delivery is based on all stock items, some non-stock products, or special-order products (such as Quickstep, Berry Alloc, Minoli tiles and bespoke order wood floors) may incur longer lead times if they require to be ordered in to stock. Please check lead times with our team before ordering.
Once your order has been placed, a staff member will contact you on the phone number and email you provided and arrange a suitable delivery date with you. This allows you to pick a date and time that is most convenient for you!
Standard delivery will be between 9am - 5pm. Our staff will instruct the courier to call you at least one hour before delivering, so you'll know when the goods will arrive. Kindly ensure the telephone number provided is the best possible number for the delivery driver to contact you on, as if the driver is unable to reach you then this may result in you missing your delivery.
We cannot give an exact time for deliveries, as the courier network may incur traffic restrictions, time delays and other unpredictable elements which makes it impossible to specify exact delivery time frame. However, the courier will have your contact number so rest assured they would not leave the property without contacting yourself or our team first.
How much does delivery cost?
UK delivery is £80, all prices are inclusive of VAT. On occasions, we run free delivery promotions online, so keep an eye out for these offers. Currently orders placed online default to a standard delivery charge, to place an order for next day, Saturday, AM or timed deliveries please contact a member of staff on 02077368789 or email sales@sqmflooring.co.uk
* Next Day delivery service is subject to stock levels and availability. Unfortunately, our next day service is unavailable for Highlands & Scottish Islands, Isle of Man and the Channel Islands.
Additional services (charges apply in addition to your delivery costs above):
Certain areas of the UK, including the Channel Islands, Isle of Man, Isle of Wight, Hebrides and Stornoway will be subject to a delivery surcharge. Please contact for further information.
How is my flooring delivered?
All deliveries are kerbside. This means that it is your responsibility or someone able) must be home to take the products from the vehicle to your home. The driver will only unload to the kerbside. Delivery drivers are not insured to enter your home. Deliveries cannot be left outside in porches, garages or any other location.
London Wooden Floor Store Ltd T/A Square Metre Flooring cannot accepted accept any liability for costs caused by late deliveries or for any other reason. We advise against booking trades for installations until goods have been received, checked and accepted on site by the customer.
Please be aware that the delivery drivers cannot stop on a red-route area as this act is illegal. Red-routes are rigorously patrolled by police and other law enforcement officials. Other arrangements will have to be made by the customer to make sure goods can be delivered successfully to properties within a red route area.
It is important that the customer does not refuse a delivery. We cannot be held responsible for any re-delivery charges or fees incurred because the customer has refused delivery.
What happens if my delivery is damaged?
We give great care and attention to your order once it has been placed. The condition of your order is hugely important and we will deliver your floor to you in the best condition possible, as you would expect.
Upon receipt of your flooring delivery, please ensure that you inspect the goods immediately and satisfy yourself that the goods are delivered in perfect condition.
In the unlikely event that a delivered product is damaged, claims can only be made if this was reported and noted on the delivery note on the day of thedelivery. London Wooden Floor Store Ltd T/A Square Metre Flooring will not be liable for any claims made after delivery or if damage was not noted on delivery note on the day of the delivery. Contact our team immediately at sales@sqmflooring.co.uk
Please note that no claim for damage can be entertained once the delivery driver has left the delivery address and signed that the floors were delievered in perfect condition. therefore it is very important that both the customer and the driver both sign for the delivery as damaged. In the unlikely event that some of your goods are damaged we will liaise with you to collect and replace the products. Any claims must be made within 7 days of receipt of goods.
You have other queries?
Remember if you need any help or guidance, kindly get in touch so one of our very helpful team members can help you.
Phone: 02077368789
Email: sales@sqmflooring.co.uk
EXCHANGE AND OUR NO FUSS REFUND
We are confident that you will love your floor as much as we do. Unfortunately, we do not offer any returns or refunds once the flooring has been fitted. Read our Terms and Conditions document for more information.
Your right to cancel
You have the right to cancel your purchase within 14 days without giving any reason.
The cancellation period will expire after 14 days from the day on which you acquire, or a third party other than the carrier and indicated by you acquires, physical possession of the goods.
To exercise the right to cancel, kindly contact us 02077368789 or by emailing sales@sqmflooring.co.uk
We operate a blanket policy that ALL deposits are non-refundable.
We will reimburse all payments received upon cancellation and upon receipt of the goods being supplied back from you. The refund will be given using the same payment method used to purchase the goods, and you will not incur any fees as a result of the reimbursement. Refunds can take up to 72 hours to be processed back into your account. Should you pass the 72-hour period without a refund being made please contact a member of our team immediately. We may make a deduction from the reimbursement for loss in value or damage of any goods supplied, if the loss is the result of unnecessary handling by you.
All goods must be re-packed by the customer as they were received. You will be responsible for paying the direct cost of returning the goods. The charge will be clearly stated to you before collection is arranged and this amount will be deducted from your reimbursement total. Once the goods have been returned to us, and have been inspected for damages, it can take up to 72 hours for your refund to be processed back to your original payment method. Please note, none of the terms & conditions stated affect your statutory rights. We cannot accept returns on products after 30 days of delivery date as batches in stock can change continually.
Faulty and Damaged Goods
In the unlikely event that a delivered product (including special order and bespoke items) is faulty or damaged, we will exchange or provide you with a full refund, as long as we are notified of the damage within 7 days of it being delivered to you.
To arrange for the goods to be collected, please email sales@sqmflooring.co.uk or call us on 02077368789 with your order number. We will collect it at no expense to you, and either provide a replacement or process a full refund.
If you find you’ve ordered a little too much for your project, you can return any unopened packs to us. The unused and unopened packs must be returned within 30 days of delivery for batch colour variation purposes. A 25% re-stocking fee will be applied and customer must also pay the cost of shipping it back to the warehouse.
Fitting Services
OpenClose
We are your partners in your flooring journey and offer the entire spectrum of support you will need to get your project done.
We offer a free site consultation and fitting services in London and Surrey. We can fit your floor, no matter the quantity in London, however, we have got a minimum order quantity outside of London for logistics and cost reasons.
Our fitting teams have a combine industry knowledge of 100’s of years fitting, revarnishing and sanding floors. We use state of the art equipment and all our installation comes with 1 year labour guarantee for peace of mind.
We offer the following services:
- Free site consultations
- Floor installation: Both floating and glue down installation
- Acoustic noise reduction using underlays or acoustilay boards depending on the complexity of your project
- Site preparation including subfloor preparation, screeding, Damp proofing, floor levelling etc
- Building a completely new subfloor if required.
- Trimming doors and architraves to meet new flooring height if needed
- Supply and installation of all flooring trims including ramps, twin profiles, skirting, beading, stair nosing etc.
- Stair cladding and installation using natural wood including installing stair nosing etc if required.
- Supply and Installation of both water and electric Underfloor Heating
Contact us today for your free no-fuss site visit and estimate:
Email: sales@sqmflooring.co.uk
Phone: 02077368789
Address: 875 Fulham Road, London. SW6 5HP.